Properties and behavioral laws of plastics
In order to be optimized, the plastic melt injection phase requires rigorous calculations...
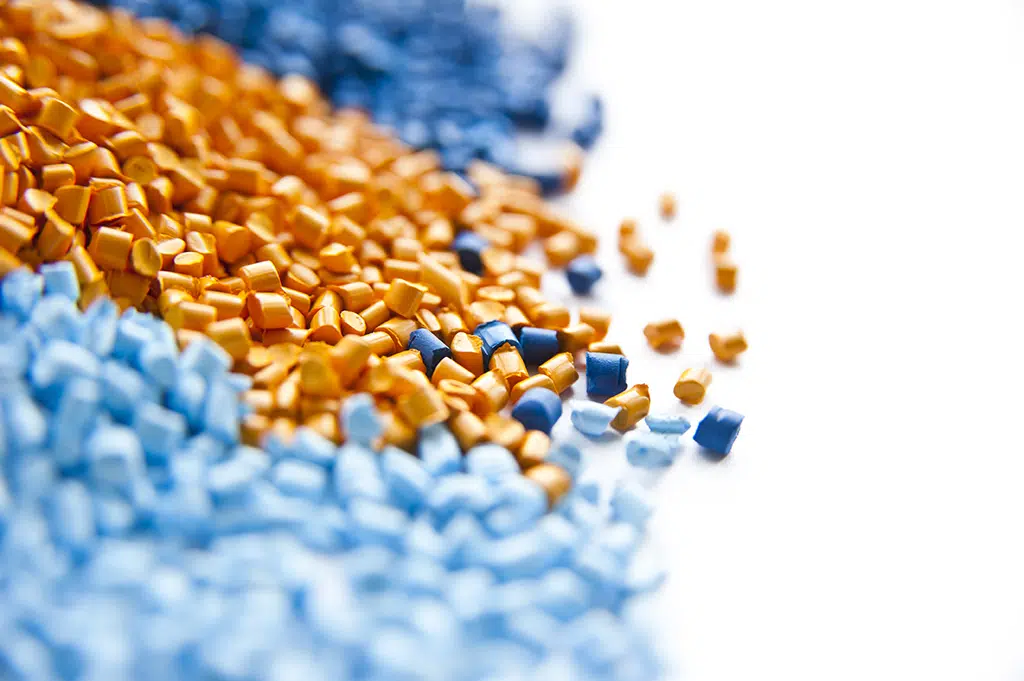
Overall, the main stages in the injection cycle are plasticizing, filling, holding and cooling.
In order to be optimized, the molten plastic injection phase requires rigorous calculations, as it has a direct influence on the characteristics of the finished part and the manufacturing method used. By studying the thermal, mechanical, morphological and rheological stresses exerted on a material, we can predict the strengths and weaknesses of a polymer part during the design phase.
The behavioral laws of matter, studied in materials science and in particular in continuum mechanics, can be used to model the behavior of fluids or solids through empirical laws of deformation. While it may seem incongruous to speak of fluid mechanics when describing the relationship between mechanical stress and deformation in solid materials, it is important not to forget that real materials can, depending on their nature and circumstances, exhibit certain aspects of fluid behavior.
Perfect fluids and viscous fluids, compressible or incompressible, these phenomena of elastic, reversible and instantaneous behavior, governed by Hooke's law, are therefore part, at least as a limiting case, of the universe of structural calculations carried out in the design office atEDELTAMP. But as organic materials, polymers and plastics have, with a few exceptions, a much lower thermal stability than metals, especially in contact with oxygen. It's worth remembering that polymers do not obey Hooke's law, and have a so-called viscoelastic behavior.
When heated to increasingly high temperatures, thermoplastic materials slowly change from a more or less rigid solid state to a highly viscous liquid. Elastic deformation, which results in a collective displacement of atoms from their equilibrium position in the case of metal, leads in the case of polymers, during elastic deformation, to an increase in structural order generated by an arrangement of macromolecular chains. Thermodynamically, this translates into an entropy reduction.
Ultimately, the final geometry of the part is a combination of all the behavioral phenomena described above. Thanks to advanced numerical optimization mechanisms, theEDELTAMP office determines the best process configurations by intelligently exploring the design space of the desired part.
Other articles in this category
Keep up to date with EDELTAMP and how we're shaping the future of the plastics industry .