TOOLING TRANSFER, INDUSTRIAL RELOCATION
Repatriating critical production resources, such as plastic injection molds, is a strategic necessity. But successfully transferring tooling without disrupting quality and deadlines is a major technical challenge. To meet these challenges, EDELTAMP has established itself as a benchmark player.
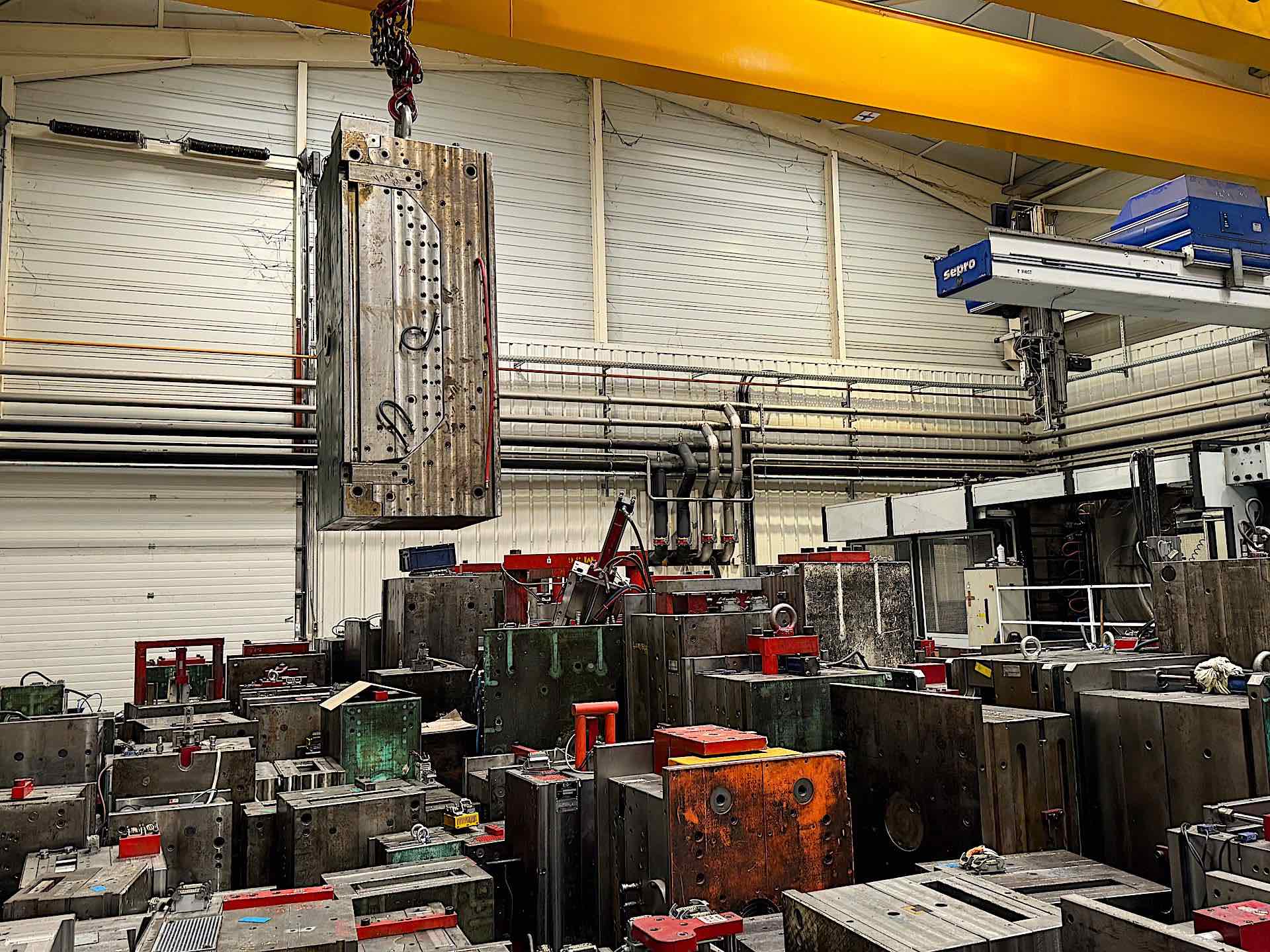
A key partner for a strategic requirement
In an industrial context marked by geopolitical instability and the vulnerability of globalized supply chains, the repatriation of critical production resources, particularly plastic injection molds, is a strategic necessity. Reducing logistical risks, securing supplies and restoring control over industrial tools are now essential levers of resilience.
But successfully transferring tooling without disrupting quality and deadlines is a major technical challenge. Faced with these challenges, EDELTAMP has established itself as a benchmark player in France, thanks to its in-depth expertise in tool transfer, return to production and quality management. The company offers manufacturers an integrated solution, from mold recovery to complete stabilization of the production process.
Tooling transfer: a methodical, secure approach
Transferring a plastic injection mold is not simply a matter of transporting equipment. Each tool is designed for a specific environment: thermal parameters, pressure, speed, specific polymer material. Altering these conditions without rigorous adaptation can lead to quality drift.
At EDELTAMPtransfer is treated as an engineering project in its own right. An in-depth initial audit is carried out on the technical data of the mold and its process (thermal range, material viscosity, geometry, number of cavities, packaging). This critical stage enables us to define the necessary adjustments and plan the supply of raw materials and specific additives.
On receipt at the Heyrieux production site, the tooling undergoes a complete mechanical and functional inspection. Each component is inspected and documented. "We anticipate adjustments through detailed mechanical analysis, to avoid failures during the rework phase", explains a technical manager.
An initial test is then scheduled, including dimensional and functional checks on the first injected parts. These samples are submitted to the customer for validation before being ramped up, guaranteeing continuity of conformity despite a change of site.
Tune-up: process requalification and optimization
The physical transfer of the mold is only the first step. The real added value ofEDELTAMP s real added value lies in its ability to requalify the tooling and stabilize the injection process within an optimized timeframe.
Each transferred mold is treated according to the qualification standards of a new mold. Development tests are carried out exhaustively: optimization of injection parameters, evaluation of thermomechanical constraints, adjustment of feed and discharge zones. "We consider each transferred mold as a new industrial integration", emphasizes the quality team.
This applies not only to part geometry, but also to appearance, surface treatments, functional performance and packaging/labeling requirements. Each customer specification is integrated into the overall quality plan.
Our combined expertise in injection molding and mold maintenance is a differentiating asset. With its own repair workshops, EDELTAMP can take immediate corrective or preventive action to extend tool life. This reactivity guarantees production continuity and a reduction in unplanned stoppages.
Training and skills transfer: securing operability
A successful transfer of tooling also involves upgrading the skills of the operating teams at the new site. EDELTAMP supports this critical phase by training its staff in the specific features of the transferred tooling: molding parameter settings, preventive and curative maintenance procedures, quality control.
This transfer of know-how is essential to preserve the reproducibility and efficiency of the process, and limit errors during the first production batches.
Time and cost management: budget control and planning
A prolonged production stoppage during a transfer can result in significant losses. EDELTAMP integrates rigorous management of deadlines and costs upstream of the project. Each stage is planned to minimize interruptions: logistical preparation, provision of technical resources, coordination of testing.
The costs of transport, any technical modifications, validation tests and training are budgeted right from the initial audit, guaranteeing financial transparency for the customer.
Post-transfer quality assurance: validation and reliability
After the transfer, EDELTAMP implements production trials in real-life conditions to validate the tooling's performance in its new environment. Strict quality controls are applied to the first production runs to guarantee dimensional, functional and aesthetic conformity.
This post-transfer validation protocol secures the resumption of series production and protects the supply chain from initial non-conformities.
Global expertise for industrial performance
With over 30 years of combined experience, the experts atEDELTAMP experts are involved in the entire tooling lifecycle: design, transfer, adaptation, maintenance and repair. This global expertise enables them to offer tailor-made solutions, adapted to the specific constraints of each customer.
In a context where industrial agility is becoming a lever for competitiveness, EDELTAMP embodies technical excellence and operational adaptability.
Its expertise in tooling transfer, re-production and quality management makes it a key partner in helping manufacturers meet the challenges of relocating and securing supply chains.
A demonstration that sustainable industrial performance relies as much on proximity and expertise as it does on technical innovation and human commitment.
Other articles in this category
Keep up to date with EDELTAMP and how we're shaping the future of the plastics industry .